The Elanco Spiral Heat Exchanger is a piece of engineering brilliance which effectively transfers heat between fluids. Engineered spiral channels guide fluid streams, allowing them to flow opposite each other and enabling efficient heat exchange. Surprisingly, despite its complex role, this device plays out its duties in a variety of settings from big factories to small businesses. Lastly, the delicacy in designing these heat exchangers mirrors the art of sculpting a round bottom flask, a tool used by experimenters in labs. It’s on with the journey to discover more about this marvelous equipment’s design features.
Elanco Spiral Heat Exchangers offer a range of benefits, such as high efficiency heat transfer, the capability to handle high solids applications, and various flow patterns to meet diverse heat transfer needs. With options for different materials and designs, Elanco Spiral Heat Exchangers provide versatile solutions for industries requiring effective heat exchange systems.
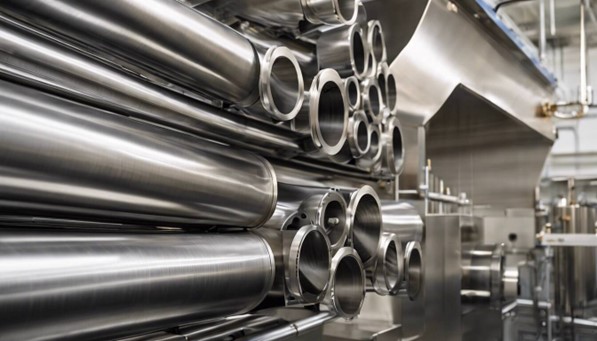
What is the Elanco Spiral Heat Exchanger?
The Elanco Spiral Heat Exchanger is a masterpiece of engineering, designed to handle the most challenging heat transfer applications with finesse and efficiency. It’s a bit like a puzzle – at first glance, it may seem simple, but it’s actually a complex and ingenious solution to demanding heat transfer requirements. Let’s uncover the magic behind this exceptional heat exchanger.
The core of the Elanco Spiral Heat Exchanger is its intricate network of spiral channels. These precisely engineered channels allow two fluid streams to flow in counter-current directions. When you hear “counter-current,” think of two people walking towards each other from opposite ends of a corridor. In the case of the heat exchanger, this counter-current flow sets the stage for remarkable heat transfer efficiency between the two fluids.
Efficient Heat Transfer
Imagine two fluid streams passing through these spiral channels—let’s say one stream is hot and the other is cold. As they flow in opposite directions, heat is effectively transferred from the hot fluid to the cold fluid. This efficient transfer of heat occurs without the two fluids mixing together. It’s like a perfectly choreographed dance where each fluid retains its unique characteristics while exchanging heat energy.
Versatility
What makes the Elanco Spiral Heat Exchanger truly remarkable is its adaptability to a wide range of operating conditions. Whether it’s handling aggressive chemicals in an industrial setting or ensuring precise temperature control in a commercial application, this heat exchanger rises to the occasion. Its ability to perform consistently across diverse environments showcases the depth of engineering expertise behind its design.
Customized Performance
Elanco doesn’t believe in a one-size-fits-all approach when it comes to heat transfer. Each application demands tailored solutions, and that’s where Elanco shines. Their Spiral Heat Exchangers are meticulously designed and engineered to deliver optimal performance based on specific industry requirements. From fine-tuning heat transfer rates to balancing pressure drops, Elanco’s expertise ensures that their heat exchangers meet and exceed expectations.
With its exceptional design, unparalleled efficiency, and adaptability, the Elanco Spiral Heat Exchanger stands as a beacon of innovative engineering in the realm of heat transfer technology. Let’s delve deeper into the tangible benefits that this marvel brings to industrial and commercial operations.
Unique Design Features of Elanco Spiral Heat Exchangers
Elanco’s Spiral Heat Exchangers are designed with a unique spiral flow configuration, setting them apart from traditional heat exchangers. This distinctive design maximizes heat transfer coefficients while minimizing pressure drops, resulting in exceptional efficiency.
The spiral flow pattern within the heat exchanger allows for increased turbulence, ensuring a more efficient transfer of heat between the process fluid and the service fluid. This results in optimal thermal performance, making Elanco Spiral Heat Exchangers ideal for applications requiring high heat transfer rates.
Moreover, Elanco goes beyond off-the-shelf solutions by offering customized designs tailored to meet specific heat transfer and specialty requirements. Whether it’s adapting the size, shape, or material composition, Elanco ensures that their heat exchangers precisely align with the operational needs of their clients.
The ability to provide tailored designs for different applications sets Elanco apart in the competitive landscape of heat exchanger manufacturers. By creating bespoke solutions that cater to the unique demands of various industries, Elanco solidifies its position as a premier provider of heat transfer equipment. This personalized approach optimizes operational efficiency and fosters long-term partnerships with clients seeking reliable and innovative heat exchange solutions.
By integrating a spiral flow configuration and offering customized designs, Elanco sets a new standard for efficiency and adaptability in the realm of heat exchangers. These distinct design features empower businesses across diverse sectors to optimize their thermal management processes while ensuring operational excellence.
In the next section, we will uncover the wide array of benefits derived from the efficiency and performance of Elanco’s Spiral Heat Exchangers. This will shed light on how these design features translate into real-world advantages for industries relying on superior thermal management solutions.
Uncovering the Benefits: Efficiency and Performance
When it comes to heat exchangers, two things are crucial: efficiency and performance. Elanco Spiral Heat Exchangers excel in both with their innovative design. Let’s take a closer look at the key advantages they offer.
Superior Heat Transfer Efficiency
Elanco Spiral Heat Exchangers are engineered to enhance heat transfer efficiency remarkably. The multiple layers of spirally wound plates create a larger surface area for heat exchange, allowing for more efficient thermal performance compared to traditional heat exchangers. This means they can effectively transfer heat between two mediums while minimizing energy consumption.
The counter-current flow pattern enabled by the spiral plate design further contributes to heightened thermal efficiency. This means that the two mediums flowing through the heat exchanger move in opposite directions, maximizing the temperature difference between them and thus improving the overall heat transfer process.
Compact Design for Space Optimization
One standout feature of Elanco Spiral Heat Exchangers is their compact footprint, allowing for efficient utilization of space. Whether within industrial facilities or commercial buildings, the ability to maximize heat exchange in a smaller area is advantageous for versatile installation options.
Minimized Fouling and Maintenance
Fouling and clogging are common issues encountered in heat exchanger systems, leading to decreased operational efficiency and increased maintenance requirements. However, Elanco’s Spiral Heat Exchanger design is adept at minimizing these challenges, reducing fouling and clogging tendencies. This benefit translates into improved reliability and reduced downtime, enhancing the overall performance and longevity of the heat exchanger system.
The reduced fouling and maintenance inherent in the design of Elanco Spiral Heat Exchangers contribute significantly to their cost-effectiveness and operational reliability.
With superior heat transfer efficiency, space-optimized design, and minimized maintenance needs, Elanco Spiral Heat Exchangers stand out as a compelling solution for businesses seeking reliable and efficient heat exchange systems.
Industrial and Commercial Applications
Elanco Spiral Heat Exchangers are like the unsung heroes running behind the scenes in various industrial and commercial sectors, quietly supporting crucial processes. These innovative heat exchangers are the go-to solution for a range of critical applications across multiple industries. Let’s explore some of the key sectors that greatly benefit from the efficiency and adaptability of Elanco Spiral Heat Exchangers.
Chemical Processing
In the realm of chemical processing, precision and reliability are paramount. Elanco Spiral Heat Exchangers play a pivotal role in this sector by facilitating efficient heat transfer during various chemical reactions and processes. Their robust design allows them to withstand the harsh operating conditions typically found in chemical plants, ensuring consistent and optimal performance.
Petrochemical Refining
The petrochemical industry relies heavily on the seamless function of heat exchangers for a range of processes including distillation, cracking, and reforming. Elanco Spiral Heat Exchangers aid in maintaining optimal temperatures during these critical operations, contributing to the overall efficiency and productivity of petrochemical refining activities.
Food and Beverage Production
From pasteurization to sterilization, food and beverage production processes demand stringent temperature control and hygiene standards. Elanco Spiral Heat Exchangers provide exceptional thermal performance and sanitary design, making them indispensable for preserving the quality and safety of food and beverage products throughout the production chain.
Pharmaceutical Manufacturing
In pharmaceutical manufacturing, precision in temperature control is vital for maintaining the integrity of sensitive compounds and medications. Elanco Spiral Heat Exchangers are prized for their ability to ensure precise temperature management during various pharmaceutical processes, contributing to the consistent quality and efficacy of the final products.
Elanco Spiral Heat Exchangers’ versatility is remarkable as they seamlessly integrate into such diverse sectors, showcasing their adaptability across different thermal applications and operational requirements.
The adaptability and efficiency of Elanco Spiral Heat Exchangers make them an indispensable asset in each of these industries, elevating thermal management processes and contributing to enhanced productivity and product quality.
Why Elanco’s Spiral Heat Exchangers Stand Out
Elanco’s Spiral Heat Exchangers are renowned for their exceptional quality and performance. Let’s explore some of the key reasons why they stand out in the industry.
Robust Construction
The construction of Elanco’s Spiral Heat Exchangers is truly impressive. They are built to last in demanding industrial environments, ensuring longevity and reliable performance. The materials used and the design of these heat exchangers make them capable of withstanding extreme conditions that would challenge other less robust designs.
The robust construction means they can handle high pressures and temperatures, making them suitable for a wide range of industrial applications. This level of durability assures businesses that their operations will not be disrupted by equipment failure due to subpar construction.
Flexibility in Material Selection
One standout feature of Elanco’s Spiral Heat Exchangers is the flexibility in material selection. Being able to manufacture heat exchangers in various high-alloy materials such as stainless steel and AL6XN® significantly enhances their applicability across diverse operating conditions and industrial processes.
This flexibility allows businesses to tailor the material selection to their specific needs based on factors such as the type of fluids being processed, temperature variations, corrosion resistance, and maintenance requirements. Whether it’s withstanding corrosive chemicals or operating in high-temperature environments, Elanco’s Spiral Heat Exchangers demonstrate adaptability and reliability.
For instance, in industries dealing with aggressive chemicals or highly corrosive substances, the choice of materials becomes critical. With Elanco’s offerings, businesses have the freedom to select the most suitable material for their specific operational environment, ensuring maximum efficiency and longevity of the heat exchanger.
These innovative features showcase why Elanco’s Spiral Heat Exchangers are sought after in various industries for their exceptional durability, flexibility, and superb performance across a wide array of applications.
The unparalleled efficiency and adaptability of Elanco’s Spiral Heat Exchangers is just one piece of the puzzle when considering heat exchange solutions for industrial processes. Now, let’s delve into the economic aspects and maintenance considerations that make these heat exchangers a wise investment.
Cost Effectiveness and Maintenance Considerations
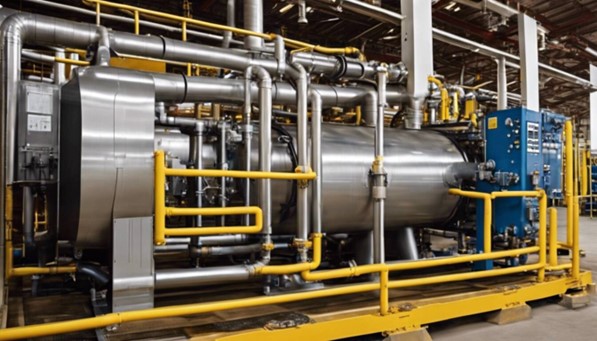
When considering an investment in equipment, the bottom line is what truly matters: cost effectiveness. That’s where Elanco’s Spiral Heat Exchangers truly shine. With their high efficiency and reduced maintenance requirements, these heat exchangers can significantly contribute to long-term cost savings for businesses.
The efficiency of Elanco’s Spiral Heat Exchangers means they transfer heat more effectively than traditional models, leading to reduced energy consumption and lower operational costs. It’s like upgrading to a more fuel-efficient car – with Elanco’s heat exchangers, you’re getting more value for your money.
Furthermore, the reduced maintenance requirements play a pivotal role in cost effectiveness. Unlike traditional heat exchangers that often require frequent maintenance due to fouling and scaling issues, Elanco’s design features minimize these problems, resulting in reduced operational downtime and lower servicing costs. This creates a win-win situation for businesses looking to optimize their operational expenses.
Consider the case of a food processing plant using traditional heat exchangers. Fouling and scaling in the heat exchanger can lead to decreased thermal efficiency, requiring frequent cleaning and maintenance. However, if the plant were to switch to Elanco’s Spiral Heat Exchanger, the reduced fouling and scaling would lead to improved thermal performance and significantly lower maintenance costs—a substantial cost-saving advantage in the long run.
It’s not just about money; it’s also about time. The ease of maintenance provided by Elanco’s design features minimizes operational downtime, allowing more time dedicated to production.
In essence, the cost effectiveness and maintenance considerations associated with Elanco’s Spiral Heat Exchangers make them an attractive choice for businesses seeking long-term efficiency and profitability in their operations.
Assessing if Elanco Spiral Heat Exchangers are the Right Choice
When it comes to selecting the appropriate heat exchanger for a particular application, several factors need to be considered. One of the primary considerations is the operating conditions. Are there extreme temperatures or pressures involved? Some heat exchangers may not perform optimally under these conditions, so it’s crucial to assess whether an Elanco Spiral Heat Exchanger is well-suited for these circumstances.
In addition to operating conditions, the required heat transfer rates must also be carefully evaluated. Different applications have varying demands for heat transfer, and it’s essential to ensure that the chosen heat exchanger can effectively meet these requirements.
Space Constraints
Space limitations can often be a restricting factor when choosing a heat exchanger. Elanco Spiral Heat Exchangers are renowned for their compact design, making them suitable for applications where space is limited. However, it’s important to analyze the available space and determine if an Elanco Spiral Heat Exchanger can be accommodated without compromising its performance.
Chemical Compatibility
The chemical compatibility of the materials used in the construction of the heat exchanger is another critical consideration. In many industrial processes, the fluids being processed may be corrosive or reactive. Therefore, it’s essential to ensure that the materials of construction of the heat exchanger are compatible with the fluids to prevent deterioration or contamination.
For instance, in industries such as chemical processing or pharmaceutical manufacturing, where aggressive chemicals or sensitive products are involved, the selection of a heat exchanger with high chemical compatibility is imperative to ensure operational integrity and product quality.
Long-Term Operational Cost Analysis
Evaluating the long-term operational costs associated with an Elanco Spiral Heat Exchanger is essential for making an informed decision. While upfront costs are a consideration, it’s equally important to assess the ongoing maintenance, energy consumption, and potential downtime costs over the lifespan of the equipment. Performing a detailed cost analysis will provide insights into the overall economic viability and sustainability of integrating Elanco Spiral Heat Exchangers into specific applications.
In essence, by thoroughly evaluating factors such as operating conditions, required heat transfer rates, space constraints, chemical compatibility, and long-term operational costs, businesses can make well-informed decisions regarding the suitability of Elanco Spiral Heat Exchangers for their specific applications. Each consideration plays a vital role in ensuring optimal performance and cost-effectiveness for integrated heating and cooling systems. When considering integrating an Elanco Spiral Heat Exchanger into your operations, carefully assessing these factors will help you make a well-informed decision regarding its suitability for your specific needs.
If you require further assistance in evaluating or acquiring an Elanco Spiral Heat Exchanger, as an authorized distributor don’t hesitate to contact us. Whether it’s for operational efficiency or adherence to industry standards, we’re here to support your endeavors.